Discover What is Porosity in Welding and Its Result on Structural Honesty
Discover What is Porosity in Welding and Its Result on Structural Honesty
Blog Article
Porosity in Welding: Identifying Common Issues and Implementing Ideal Practices for Avoidance
Porosity in welding is a prevalent concern that usually goes undetected until it triggers substantial issues with the stability of welds. In this discussion, we will certainly check out the vital variables contributing to porosity formation, analyze its damaging results on weld performance, and review the ideal techniques that can be embraced to reduce porosity incident in welding processes.
Usual Sources Of Porosity

Utilizing filthy or damp filler products can introduce contaminations right into the weld, contributing to porosity issues. To minimize these typical causes of porosity, extensive cleansing of base steels, appropriate shielding gas choice, and adherence to ideal welding parameters are essential practices in attaining high-grade, porosity-free welds.
Effect of Porosity on Weld Top Quality

The existence of porosity in welding can dramatically endanger the architectural honesty and mechanical homes of bonded joints. Porosity creates voids within the weld steel, damaging its overall stamina and load-bearing capability.
Welds with high porosity levels have a tendency to display reduced effect toughness and minimized capability to deform plastically before fracturing. Porosity can impede the weld's ability to efficiently send forces, leading to premature weld failure and prospective safety threats in important structures.
Ideal Practices for Porosity Avoidance
To improve the architectural honesty and high quality of bonded joints, what specific steps can be applied to lessen the incident of porosity during the welding process? Porosity avoidance in welding is important to make certain the honesty and stamina of the last weld. One effective practice is correct cleansing of the base metal, removing any kind of impurities such as corrosion, oil, paint, or wetness that can lead to gas entrapment. Ensuring that the welding equipment is in good problem, with clean consumables and appropriate gas circulation rates, can likewise considerably reduce porosity. In addition, preserving a stable arc and managing the welding parameters, such as voltage, present, and take a trip speed, aids develop a constant weld swimming pool that reduces the risk of gas entrapment. Using the proper welding technique for the details material being welded, such as adjusting the welding angle and gun position, can better avoid porosity. Routine inspection of welds and prompt remediation of any kind of problems determined during the welding procedure are essential practices to avoid porosity and create high-quality welds.
Relevance of Appropriate Welding Methods
Executing correct welding strategies is extremely important in making sure the architectural honesty and quality of welded joints, building on the structure of reliable porosity prevention procedures. Welding methods straight influence the general toughness and durability of the bonded structure. One key facet of correct welding methods is preserving the correct warmth input. Excessive heat can result in enhanced porosity as a result of the entrapment of gases in the weld Visit Website pool. On the other hand, insufficient warm might lead to incomplete fusion, creating prospective weak factors in the joint. In addition, using the suitable welding parameters, such as voltage, existing, and travel rate, is crucial for accomplishing sound welds with very little porosity.
Furthermore, the choice of welding procedure, whether it be MIG, TIG, or stick welding, should align with the details demands of the project to make sure optimum outcomes. Appropriate cleaning and preparation published here of the base steel, in addition to selecting the appropriate filler material, are also necessary components of skilled welding strategies. By adhering to these ideal methods, welders can minimize the threat of porosity development and generate top quality, structurally sound welds.
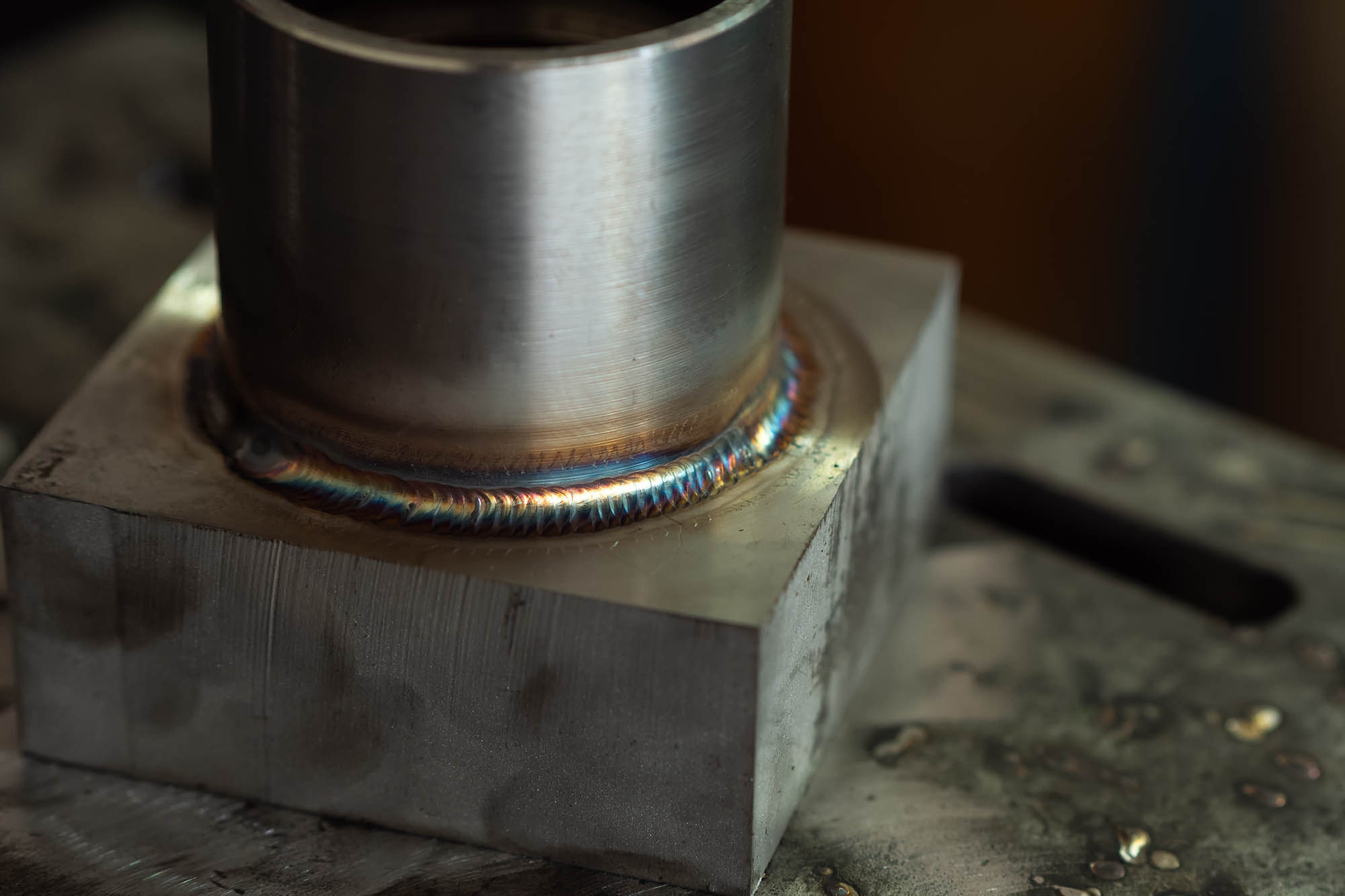
Testing and Quality Assurance Actions
Testing procedures are essential to detect and prevent porosity in welding, making certain the toughness and durability of the last item. Non-destructive screening approaches such as ultrasonic screening, radiographic testing, and aesthetic inspection are commonly utilized to identify prospective defects read what he said like porosity.
Conducting pre-weld and post-weld inspections is additionally important in maintaining quality assurance standards. Pre-weld assessments include verifying the materials, equipment settings, and sanitation of the workplace to stop contamination. Post-weld evaluations, on the various other hand, examine the last weld for any defects, consisting of porosity, and confirm that it fulfills defined criteria. Executing a thorough high quality control plan that includes detailed testing treatments and inspections is critical to lowering porosity concerns and making certain the total quality of welded joints.
Final Thought
To conclude, porosity in welding can be a common problem that affects the quality of welds. By recognizing the usual root causes of porosity and carrying out ideal practices for prevention, such as appropriate welding strategies and testing measures, welders can ensure high quality and reputable welds. It is essential to prioritize prevention methods to decrease the occurrence of porosity and maintain the honesty of welded frameworks.
Report this page